Aircraft cables are stranded wires that are used in a wide variety of applications on or around aircraft. For example, they are used as harnesses for electrical wiring, tie-downs, stabilizers, safety fasteners, and many other purposes. Read More…
As leading innovative wire rope manufacturers, Bergen Cable Technology has been providing engineering assistance for well over half a century, helping customers develop cost effective, durable solutions.
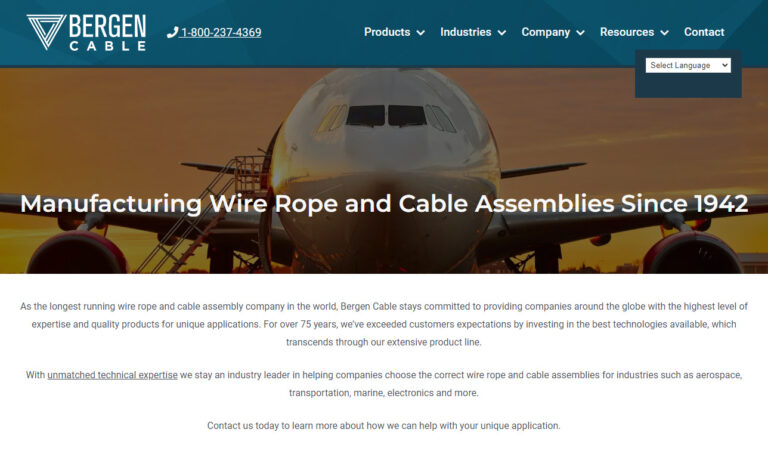
JSC, as one of the most diversified wire rope manufacturers, utilizes over 200 production machines to produce top rated wire products in ferrous and nonferrous materials. Industries that JSC serves include electronics, geophysical and communications.
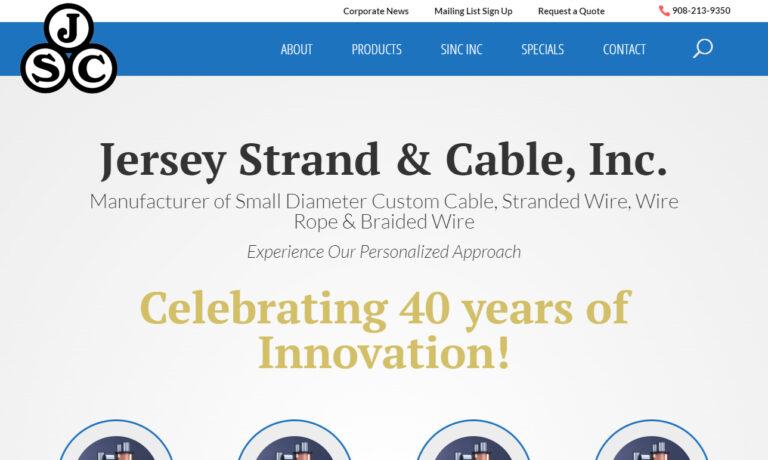
Lexco is an ISO:9001 manufacturer of wire rope, cable, and bungee cord assemblies; and push-pull controls. Our in-house capabilities range from swaging and extrusions to die-casting, proof-loading, and CNC machining. Lexco Cable is proud to serve a diverse set of markets including military, aerospace, OEM, MRO, marine, architectural, and more. Contact us today.
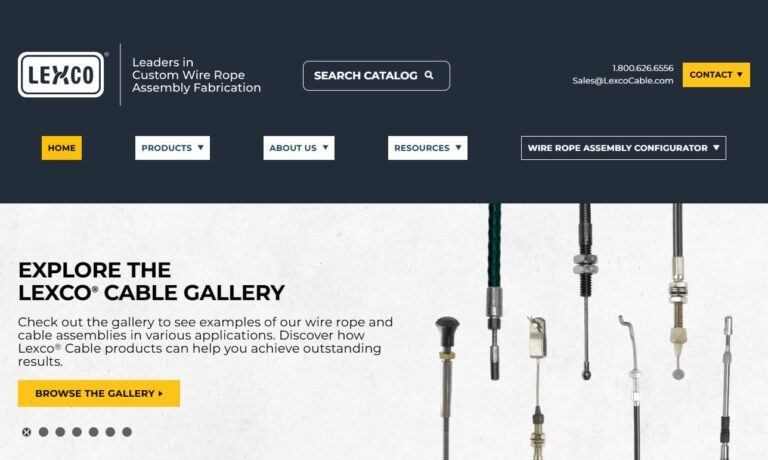
For over 30 years, companies across various markets have relied on Motion Control Technologies to provide high-quality mechanical cable solutions. Our line of products includes commercial cable lanyards, galvanized wire rope cable lanyards, swaged fittings, and more. We strive to build long-lasting relationships with our customers, regardless of your industry. Contact us today and tell us how we...
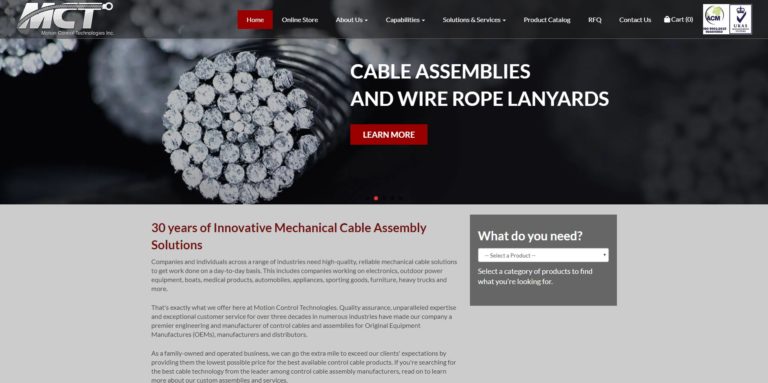
Aero Assemblies, Incorporated strives to make every effort, as dedicated wire rope manufacturers, to maximize product value throughout the manufacturing process.
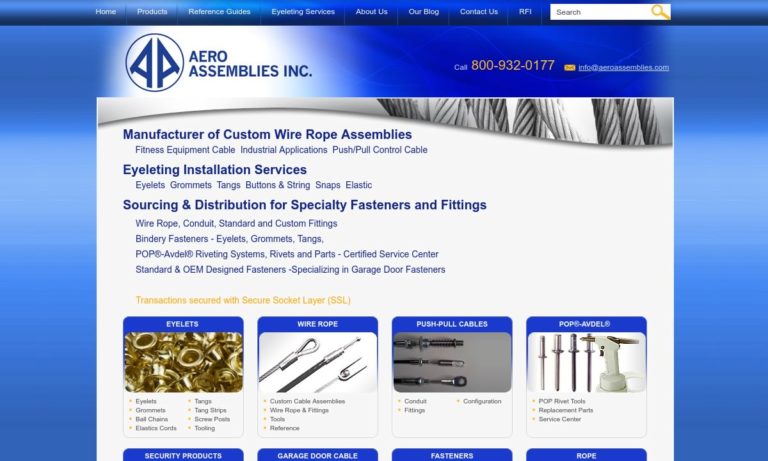
More Aircraft Cable Manufacturers
Outside of the actual aircraft, the same cables may be used as wire rope slings to lift jet engines, wings, and other components into place during assembly or repair. These specialized high-strength cables are also used as arresting gear, which stops aircraft when the landing area is limited by engaging the tail hook and transferring the kinetic energy.
While aircraft-related uses abound, aircraft cables are very versatile and used in numerous other applications where their high strength, corrosion resistance, and smaller diameters are needed. Industries such as agriculture, marine, and irrigation commonly use this type of cable, as do military and aerospace applications.

Types of Aircraft Cables
There are two main types of aircraft cable available based on material composition. The highest quality cable is made of stainless steel, either 316 or 302/304 depending on the application. Stainless steel cables offer high strength, fatigue, and corrosion resistance even in salt water or other caustic or harsh environments.
The second type, galvanized cables, are steel cables hot dipped in zinc for increased durability and corrosion resistance. These cables are an economical alternative for mild environments as the two have similar pulling strengths, but stainless steel lasts longer under harsh conditions.
Though these cables are a type of wire rope, the main distinction is that wire ropes are commonly available with diameters no smaller than 1/4 inch, while aircraft cables with diameters as small as 3/64 inch are commonly used.

Maintenance of Aircraft Cables
Temperature variations and exposure to the outdoors make life difficult for aircraft cables. They are prone to wear and degradation, as they sit in static positions around pulley bends for long periods while the plane is in flight.
Regrettably, most control system cables in aircraft are original to the aircraft and have lasted significantly longer than their intended design life. Therefore, all control cables must be inspected for damaged wire strands at every annual or 100-hour inspection. This must be done all the way down the accessible cable's length (although issues are most likely near pulleys and guides).
Any cable assembly with a single damaged wire strand in a critical fatigue location must be replaced. A critical fatigue region is defined as the length of a cable that passes over, under, or around a pulley, sleeve, or through a fair lead; any cable piece that is bent, rubbed, or manipulated in any way; or any point within one foot of a swaged-on fitting, according to FAA regulation. This method works well for detecting external cable damage.
However, environmental deterioration, distortion, fatigue, and wear can cause cables to fail from the inside out. The only way to accurately evaluate cables for interior damage is to remove them from the aircraft and manually flex them while inspecting them for damage under a magnifying lens. Because the cost of labor to remove, install, and rig aviation cables is typically higher than the cost of the cable itself, replacing control cables regularly, such as every 15 years, makes sense.
Due to the tremendous stress and risks connected with control system failures, it is recommended to change the rudder/tailwheel cables every five years for tailwheel aircraft. It's also crucial to inspect and spin the pulleys during the examination.
Rotating the pulleys allows the bearings to be inspected for wear and functionality. For example, if the bearing is frozen or the pulley is misaligned, the wear pattern on the pulley can reveal it. The pulley and cables should also be greased according to the manufacturer's instructions (if applicable).

It is recommended that an incremental replacement strategy be implemented to guarantee that any control cables that may be original to the aircraft are replaced in a reasonable amount of time. Begin with the most vital systems and replace one cable system at a time (for example, elevator cables) as funds permit.
Choosing the Proper Aircraft Cables Manufacturer
To make sure you have the most beneficial outcome when purchasing Aircraft Cables from an Aircraft Cables Manufacturer, it is important to compare at least 4 or 5 Companies using our list of Aircraft Cables manufacturers. Each Aircraft Cables Supplier has a business profile page that highlights their areas of experience and capabilities and a contact form to directly communicate with the manufacturer for more information or request a quote. Review each Aircraft Cables company website using our patented website previewer to get an idea of what each business specializes in, and then use our simple RFQ form to contact multiple Aircraft Cables businesses with the same message.