Multiple flexible wire strands are coiled in a circular pattern around a core to form braided wire, which is then wound on a spool. The wires are brought together during the weaving process and shaped into flexible, sturdy, spherical braids. Its size depends on a manufacturer's braiding machine's carrier count.Read More…
Jersey Strand & Cable, Inc.
JSC, as one of the most diversified wire braid manufacturers, utilizes over 200 production machines to produce top rated wire products in ferrous and nonferrous materials. Industries that JSC serves include electronics, geophysical and communications. Their mission is to continually improve their expertise, capabilities, products and services for current and future worldwide customers.
Phillipsburg, NJ |
800-528-3900
Request for Quote
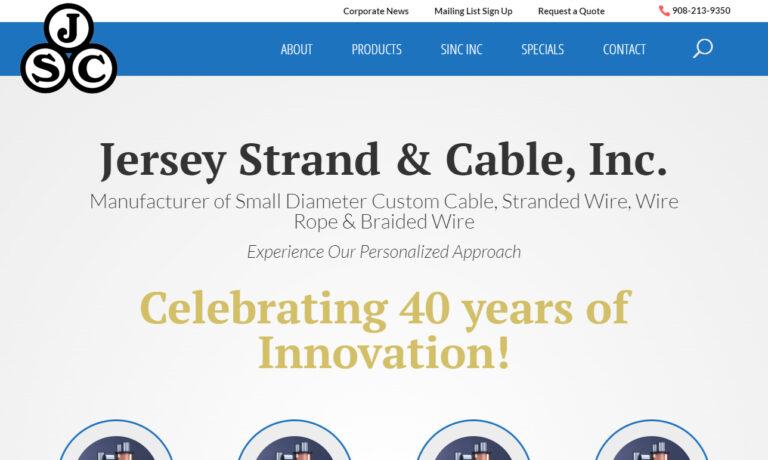
More Wire Braid Manufacturers
Braided Wire Construction
Copper, which can be bare or coated, is frequently used to make braided wire. Tinned copper is the most popular alternative, even though silver-plated and nickel-plated copper is also available because of their excellent conductivity, corrosion resistance, and soldering simplicity. Several strands of thin, flexible wire are the precursors to a braided wire.

The number of carriers the braiding machine has affects the size of a wire braid. A machine typically has sixteen, twenty-four, or forty-eight carriers. Each carrier has a bobbin that can handle one to sixteen strands of wire or more, depending on the machine. The construction information on the braid specs will reveal how many carriers and wires per carrier are used to create a specific braid. Typically, the construction is represented by three integers (for example, 24-4-36). In this case, the sequence of these numbers would represent:
- The number of carriers is 24.
- There are four wires on each carrier.
- The gauge (AWG) of each wire is 36 (some may list the diameter in mm).

A big wheel called a capstan moves the wire through the braiding machine. A pressure roller on the capstan flattens a circular braid into a flat braided wire. A flat braid has the same strength and flexibility as a round braid, but it conducts electricity with less resistance because of its wider surface area.
Several call codes identify wire braids, including the well-known AA59569 mil-spec braid, which was once subject to the QQ-B-575 military specification. Wire braid is available in both round and flat varieties. A conventional mesh tabular arrangement of multiple tiny wires is tightly woven to form the shielding surrounding the conductor. It can be flattened in some designs to attain the necessary width. A thin insulating coating covers the cable’s braid and other interior parts.
Braided Wire-Making Process
The process of creating braided wire begins with the winding of numerous strands of thin wire on quickly revolving spools. Next, the wire is woven into a string and flexible braid by the rotating spool in a circular pattern around a core.
The braiding machine’s carriers decide the wire size. It is an essential component of a braiding machine that has several uses. It secures the wire bobbin, keeps tension constant even when it breaks, and makes up for the length discrepancy.
A braiding machine can have 16, 24, or 48 carriers depending on the machine. Each carrier has a bobbin, and can carry 1–16 wire strands, possibly more.
Uses of Braided Wire
From mining to aerospace, braided wire is indispensable in many different industries. One of the braided wire’s most frequently mentioned advantages is flexibility. Its construction may move in a range that solid wire cannot work due to the weaving of the thin strands.
Tubular braided wire is a good shielding material for cables because it keeps them flexible while protecting them from corrosion, impact, and electrical fields. Copper braided wire, in particular, is extensively used in coaxial cables as a conductive barrier. In addition, modern circuits frequently use braided wires because they can withstand a wide range of voltages, including fluctuating voltages, thanks to the stranding and copper’s high conductivity.

Like its tubular cousin, a flat braided wire has a variety of applications in commercial and industrial environments. Due to its adaptability and capacity to withstand shock and vibration, it is a common choice for grounding. Given that the wider surface area of the strap has lower radio frequency (RF) resistance, it is especially helpful in radio environments. A flat braid wire is also frequently utilized in lightning protection systems. Since the braid offers lightning a low-resistance path to the ground and produces little to no heat, it is a crucial safety component. With the help of this feature, dangerous situations that could start fires are avoided, and buildings are protected from the risks of lightning strikes.
Choosing the Correct Wire Braids Manufacturer
To make sure you have the most beneficial outcome when purchasing Wire Braids from a Wire Braids Company, it is important to compare at least 4 or 5 Manufacturers using our list of Wire Braids manufacturers. Each Wire Braids Supplier has a business profile page that highlights their areas of experience and capabilities and a contact form to directly communicate with the manufacturer for more information or request a quote. Review each Wire Braids company website using our patented website previewer to get an idea of what each company specializes in, and then use our simple RFQ form to contact multiple Wire Braids companies with the same message.